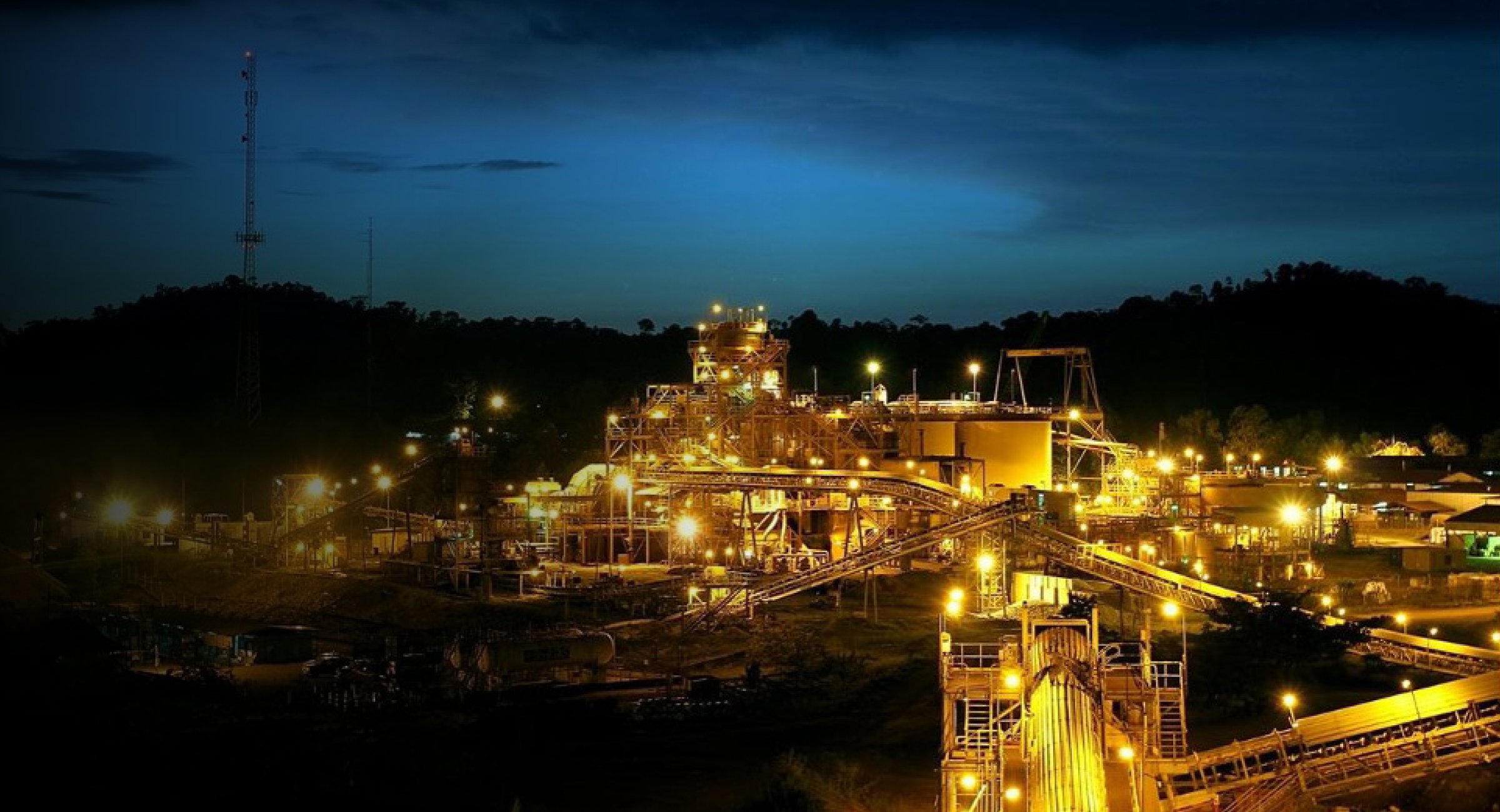
Project: Damang Gold Mine
Client: Goldfields
Location: Ghana
Overview
The Damang Gold Project is located in Ghana and is 90% owned by Goldfields Ghana, with the remaining 10% held by the Ghanaian Government.
The comminution circuit comprises tertiary crushing followed by a grinding circuit in SABC configuration. The SAG mill receives 100% tertiary crushed feed and operates in closed circuit with a pebble crusher. The SAG discharge screen undersize reports to the ball mill closed with cyclones, with partial cyclone U/F treated via a gravity circuit. The cyclone overflow reports to a pre-leach thickener prior to the CIL circuit.
Feed to the circuit is relatively consistent in competency but can have a variable grind-recovery relationship. Issues had been experienced with cyclone stability, including high underflow density, roping with grit reporting to the trash screens and high recirculating load with power draw losses in the ball mill. The client’s primary objective was to explore if increased gold recovery was achievable by producing a finer and more consistent grind without sacrificing throughput.
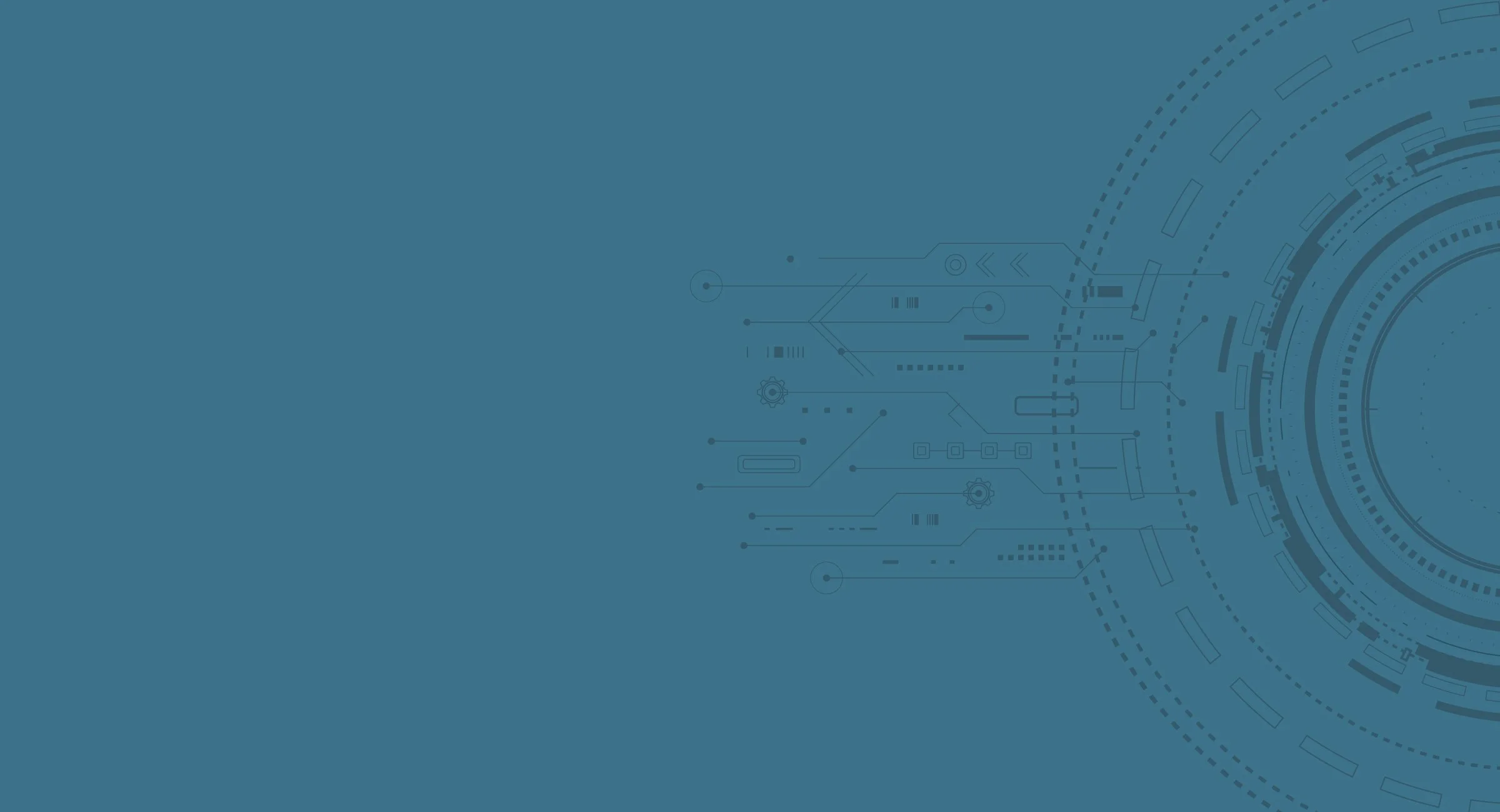
The Challenge
The client wanted to achieve a finer grind without compromising throughput efficiency improvements.
The MillROC Solution
MillROC was implemented with a live mass balance and dashboards to better understand the circuit constraints. The MillROC consultant was then engaged to develop an optimisation plan to assist in achieving the site’s targets for the comminution circuit. The plan was split into three categories:
Phase 1 – Stabilisation Control. The engagement focused on coaching to achieve plant stability. Key focus areas included mill density, power draw, cyclone pressure control / circulating load and grind. The process control strategy was also optimised.
Phase 2 – Optimisation. The second stage focused on controlling grind vs throughput and optimising circuit set-points. As part of this process, adjustments were made to the SAG mill discharge grate and screen apertures. The ball mill ball top-size was adjusted, and the ball addition rate optimised.
Long-term items – Long-lead item optimisation strategies were identified and prioritised, with support provided over time as each item was implemented.
Outcome
Grind P80 reduced by 24.6%. Grind sensitive ore show 2% improvement in recovery.
5.7% increase in throughput.
7.6% improvement in energy efficiency.
Improved circuit stability, greatly reducing incidences of cyclone roping operator intervention
See conference paper for more details – SAG 2023